Defects of spray welding
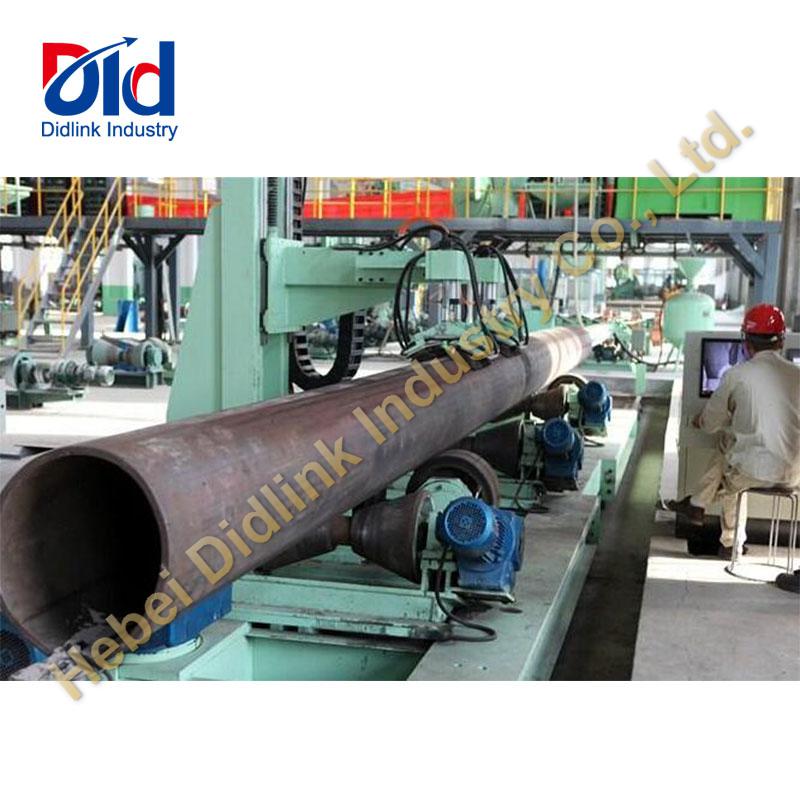
1 Spalling of spray welding layer
The spalling phenomenon of spray welding layer is mostly found in the process of machining. The main reason is that the coating remelting operation speed is too fast, the substrate surface is not heated to the melting or semi melting state, the spray welding layer and the workpiece surface can not form metallurgical bonding, but the adhesion between molecules. In addition, if the preheating temperature of the workpiece is too high, oxide film will be formed on the surface of the workpiece; the surface preparation of the workpiece is not qualified; the thickness of the coating is uneven, the brittleness of the spray welding alloy is large, and the melting point is too low.
For the workpiece with local spalling of spray welding layer, the spray welding layer can be remelted according to the process requirements, and then spray welded to the required thickness. In case of serious spalling of spray welding layer, it is necessary to turn off and spray weld again.
2 Spray welding layer crack
The common fracture and cracking of spray welding layer mostly occurred in the cooling process, but also occurred in the use process. Cracks rarely extend to the base metal. The reason of crack is that the expansion coefficient difference between spray welding alloy and base metal is too big, the preheating temperature before welding is too low and the cooling speed is too fast after welding. In addition to the preheating and slow cooling measures mentioned above, if necessary, a layer of plastic material with good plasticity can be used as the transition layer on the substrate surface.
When cracks occur after welding, the workpiece is allowed to be reheated and remelted again, and the melting should be thorough. The preheating temperature can be properly increased, generally 400 ~ 500 ℃.
3 Blowhole of spray welding layer
There are oxide film, rust, oil stain on the surface of the workpiece, or oxidation of the alloy powder on the surface of the workpiece, which will cause Blowholes in the spray welding layer. Therefore, the surface of the workpiece to be welded must be kept clean, and the nature of the flame should be strictly controlled when spraying. The results of overheating or excessive melting of the workpiece surface will also cause blistering of the spray welding layer. At this time, it is necessary to move the flame away quickly to reduce the temperature of the molten pool and the workpiece surface, and then melt again to make the gas in the spray welding layer escape. When the spray coating is remelted too quickly or the flame suddenly approaches the coating surface, the gas in the coating can not escape in time.
4 Slag inclusion
The formation of slag inclusion is related to remelting operation. During remelting, the flame moves too fast, the slag is not completely floating out, and the molten pool has solidified to form slag inclusion. The oxidation impurities on the surface of the workpiece will directly hinder the fusion between the spray welding layer alloy and the substrate, and there are often discontinuous chain like slag inclusions on the fusion line. It is difficult to eliminate these slag inclusions by scum method. Therefore, the surface to be welded should be prepared in strict accordance with the above conditions.