How Check Valve Operation ?
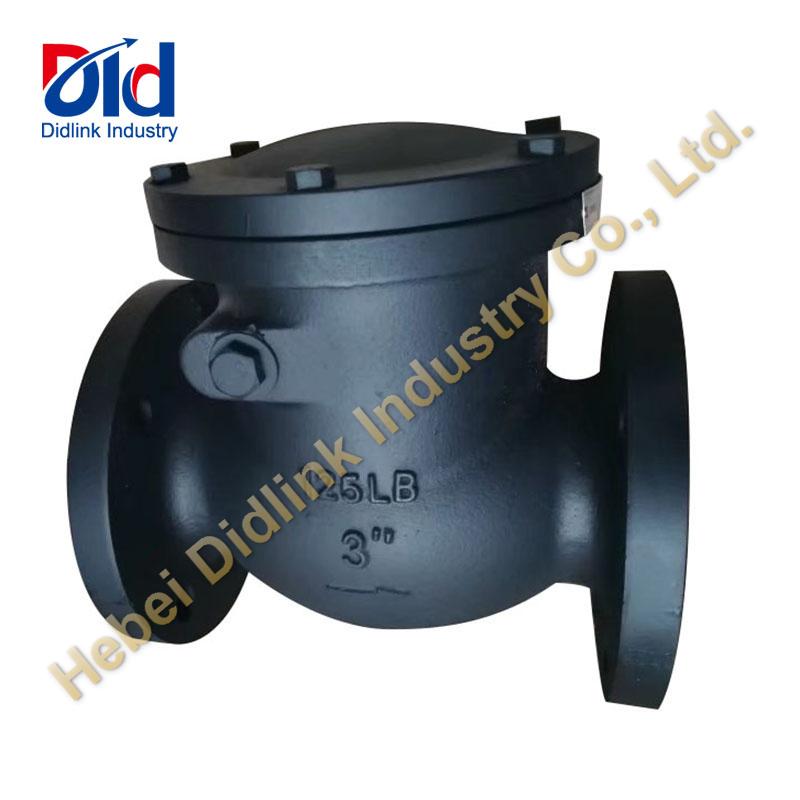
Check valves are flow sensitive and rely on the line fluid to open and close. The internal disc allows flow to pass forward, which opens the valve. The disc begins closing the valve as forward flow decreases or is reversed, depending on the design. Construction is normally simple with only a few components such as the body, seat, disc, and cover. Depending on design, there may be other items such as a stem, hinge pin, disc arm, spring, ball, and bearings.
Internal sealing of the check valve disc and seat relies on fluid back-pressure as opposed to the mechanical force used for on/off valves. Because of this, allowable seat leakage rates are greater for check valves than for on/off valves. Metal sealing surfaces generally will allow some leakage while elastomers, such as Buna-N and Viton, provide bubble-tight shutoff (zero leakage). Because of this, elastomers should be considered for air/gas media, where chemically compatible, and low-pressure sealing.
Among the many factors to consider when selecting a check valve are material compatibility with the medium; valve rating (ANSI); line size; application data (flow, design/operating conditions); installation (horizontal, vertical flow up or down); end connection; envelope dimensions, especially if replacing an existing valve to avoid pipe modifications; leakage requirements; and special requirements such as oxygen cleaning, NSF, NACE, CE Mark, etc.