Valve manufacturing process characteristics
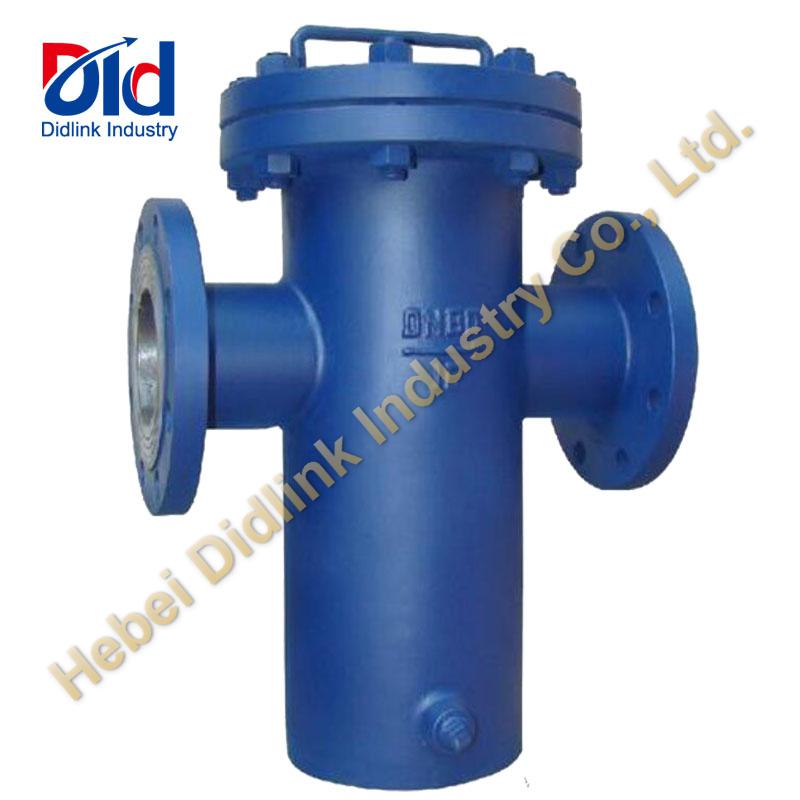
At first glance, there are not many valve parts, simple structure, and general accuracy. They are simple parts in the machinery industry, but the core sealing parts of the valve are particularly demanding. The valve manufacturing process is complicated and the technical difficulty is also great. What process characteristics should we pay attention to?
1. Manufacturing materials
Due to the wide variety of valves and specifications, they are used in various fields of the national economy, and their use occasions vary widely, such as high temperature and high pressure, low temperature and cryogenic temperature, flammable and explosive, highly toxic, and highly corrosive media. Demanding requirements.
In addition to cast iron, carbon steel, alloy structural steel, a large number of CrNi stainless steel, CrMoAl nitriding steel, CrMoV heat resistant steel, CrMnN acid resistant steel, precipitation hardening steel, duplex stainless steel, low temperature steel, titanium alloy, Monel alloy , Inconel, Hastelloy and G0CrW cemented carbide. These high-alloy materials have poor casting, welding, and processing performance, which brings great difficulty to the manufacturing process. In addition, most of these materials are expensive materials with high alloy, high strength and high hardness. There are many difficulties in the selection, preparation and procurement of materials. Some materials are difficult to purchase and supply due to the small amount of use.
2. The structure of the casting blank
Most of the valve blanks are made of thin shell castings with complex structures, which not only require good appearance quality, but also have dense internal quality and good metallographic structure, and must not have defects such as pores, shrinkage holes, sand inclusions, cracks, etc. . Therefore, the casting process is complicated and the heat treatment technology is difficult. In the mechanical industry, the casting of the pressure-bearing thin-shell casting blank of the valve is much more complicated and difficult than the casting of other mechanical components.
3. Mechanical processing technology
Most of the high-strength, high-hardness, and high-corrosion-resistant materials have poor cutting performance. For example, high-alloy stainless steel and acid-resistant steel have the disadvantages of high toughness, high strength, poor heat dissipation, high chip adhesion, and strong work hardening tendency. It is difficult to achieve the required dimensional accuracy and finish, which brings certain difficulties to machined tools, processes and equipment. In addition, the valve sealing surface has high requirements on machining accuracy, matching angle, smoothness and matching sealing pair, which brings great difficulty to mechanical processing.
4. Process arrangement of valve parts
The main parts of the valve are not many, the structure is relatively simple, the processing accuracy of most sizes is not high, and the exterior is relatively rough, which gives the impression of a simple machine. In fact, the heart sealing part of the valve is extremely precise. The "three degrees" (flatness, smoothness, hardness) of the sealing surface is very high, and the matching degree of the sealing pair composed of the two sealing surfaces must reach zero to zero. In order to meet the zero leakage of the airtight test. This kind of rough reference to ensure the precise zero-to-zero requirements of the heart is the biggest technical difficulty of valve processing.
5. Valve test and inspection
Valves are important opening and closing and regulating components of pressure pipelines, and the working conditions of pressure pipelines are very different, high temperature and high pressure, low temperature and deep cold, flammable and explosive, highly toxic and strong corrosion. However, the test and inspection conditions of valve manufacturing cannot reach the same requirements of the working conditions. Various international and domestic valve test standards stipulate that the test is performed under the conditions near normal temperature, using gas or water as the medium. This has the most fundamental hidden danger, that is, the valve products that pass the normal factory test. Under harsh actual working conditions, it may be difficult to meet the use requirements due to problems such as material selection, casting quality, and seal damage. Quality accidents.