Safety valve performance requirements
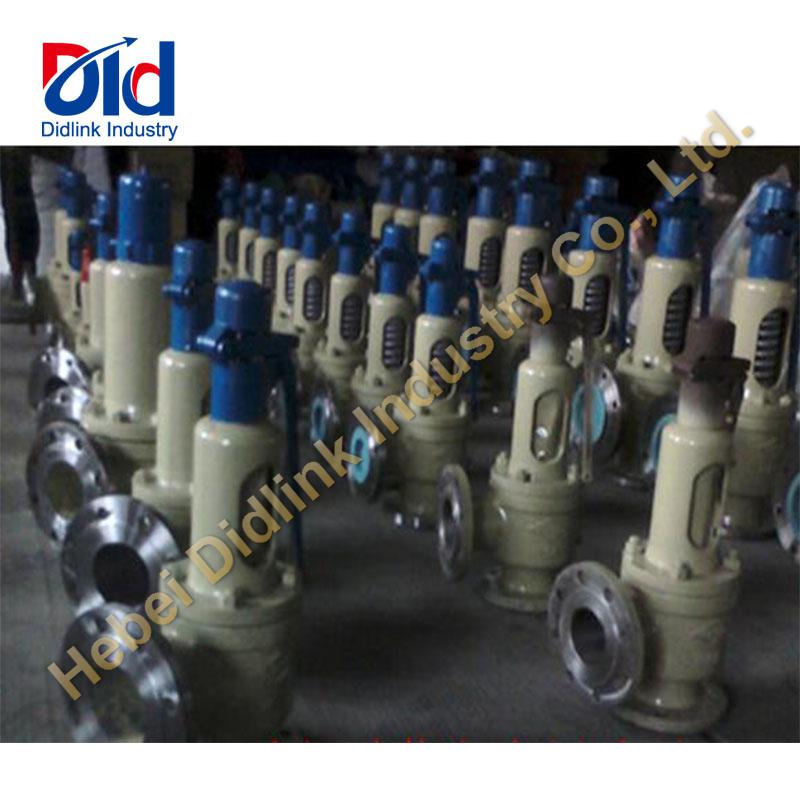
The safety valve is a safety device used to prevent the pressure in the pressure equipment from exceeding the allowable value. The function of the safety valve is realized by the following action process: When the system reaches the maximum allowable pressure, the safety valve can open accurately, and quickly reach the rated opening height, and discharge the rated amount of working medium; the safety valve is in the open state The discharge should be stable; when the system pressure drops to a certain value, the safety valve should be closed in time, and in the closed state, it must be kept in a sealed type. The following describes the basic performance requirements of safety valves.
1. Open accurately
The safety valve should reliably open to the specified opening height under the predetermined pressure and reach the specified discharge capacity. This is the basic requirement for the safety valve. That is, when the inlet pressure of the safety valve reaches the predetermined set pressure, the safety valve should open accurately and quickly reach the specified opening height.
When the pressure in the system reaches the maximum allowable pressure, the insensitive response of the safety valve to the increase in pressure will lead to dangerous situations such as rupture and damage of boilers, pressure vessels and pipelines. Especially for compressible gas media, the danger is higher.
The set pressure of the safety valve should not be greater than the design pressure value of the boiler, pressure vessel and pipeline.
The deviation of the positive pressure of the safety valve is clearly stipulated in the relevant regulations and standards. When the safety valve is adjusted for the setting pressure, its deviation should be strictly controlled within the specified range.
2. Stable emissions
After the safety valve reaches the specified opening height, it maintains a stable discharge state and can discharge a rated amount of working medium. There should be good mechanical properties (no frequency jump, chatter, etc.) during the medium discharge process. This requirement is very important.
The safety valve should have a reasonable structure and a spring with a reasonable stiffness to maintain good mechanical characteristics and stable discharge capacity. The size of the flow passage of the safety valve should meet the required parameter requirements for the calculation. If the cross-sectional area of the flow passage is too small, after the safety valve is opened, the overpressure part of the medium cannot be discharged in time, and the system pressure continues to rise, which is very dangerous. On the contrary, if the cross-sectional area of the flow passage is too large, after the safety valve is opened, the pressure will drop sharply below the working pressure, and the safety valve disc will close and cause a violent impact on the valve seat; however, because the system pressure rise factor has not been eliminated, the disc will again Open to form a frequency jump, and as a result, the valve seat and the sealing surface of the disc will be damaged due to repeated impacts. When safety valves are used for incompressible liquids, frequency jumps may also cause water hammer in the system.
The inlet pressure of the safety valve when it reaches the rated opening height is called the discharge pressure. It is used in different media or the same media under different working conditions, and its rated discharge pressure is different, which is clearly stipulated in relevant regulations and standards. It is usually expressed as the percentage of the set pressure exceeding the value. The structural design of the safety valve should ensure that the rated discharge pressure is strictly controlled within the specified range.
3. Close in time
When the discharge of the safety valve reduces the medium pressure to a certain value, the valve flap falls into contact with the sealing surface of the valve seat and reaches the closed state again. The safety valve can be seated and closed in time and effectively, which is an important indicator of good performance.
The action of the safety valve does not necessarily require the equipment or system to stop running or to be repaired. Sometimes, the action of the safety valve is caused by accidental factors such as misoperation in the system. In this case, it is not desirable that the return pressure of the safety valve is too much lower than the working pressure. Too low return pressure means excessive loss of energy and medium, and disrupts the normal operation of the entire system. On the contrary, the seat back pressure is not too high. If the return pressure is close to the opening pressure, it is easy to cause the safety valve to reopen, causing the safety valve to jump frequently, and it is not conducive to re-establishing the seal after closing. In addition, in the case that the safety valve cannot be closed reliably, since the medium between the sealing surfaces is not completely cut off, it is impossible to restore the sealing performance under the normal working pressure of the system.
The design of the safety valve should ensure that it can be closed quickly and effectively. Quick and powerful seat return is more conducive to the establishment of sealability than gradual and slow seat return.
The seat return performance of the safety valve is relatively measured by the opening pressure value, which is generally determined by the opening and closing pressure difference. Safety Valves used for different media have different opening and closing pressure differences, which are clearly stipulated in relevant regulations and standards.
4. Reliable sealing
When the protected system is at normal operating pressure, the closed safety valve has good and reliable sealing performance. Because the safety valve leaks, the working medium (sometimes very expensive or dangerous medium) will be lost, energy consumption will be increased, and the surrounding environment and atmosphere will be polluted by the working medium. Excessive leakage will even affect the normal operation of the equipment or system, and even force the device to stop running. Continuous leakage will also corrode the sealing surface of the safety valve, resulting in complete failure of the safety valve.
Re-establishing the seal after the safety valve is operated is more difficult than maintaining the original seal state. Because the safety valve is closed, the medium pressure acts on the larger area of the valve disc, but before opening, it only acts on the smaller area restricted by the sealing surface. Therefore, the sealing performance of the safety valve is likely to be reduced after the operation, and thus is lost. In particular, it is more difficult to solve the back-seat seal of the direct load acting safety valve. In safety valves with auxiliary operating mechanisms, this problem is solved by means of forced sealing.
It is more difficult to require safety valves to maintain tightness than valves generally used for shut-off valves. Because there is no great force applied between the seals, the safety valve disc clings to the valve seat only to form a seal pressure with a small seal specific pressure. The sealing pressure is determined by the difference between the setting pressure of the safety valve and the operating pressure of the equipment, usually a small value (usually 10% of the setting pressure), so the size and surface roughness of the sealing surface of the safety valve are required Very strict.
The requirements for the tightness of the safety valve vary depending on the medium or working conditions. Generally speaking, it is difficult to achieve a safety valve with a metal-metal sealing surface to achieve no leakage. The safety valve with a soft sealing structure of metal-nonmetal has much better sealing performance.